RFID for Supply
Chain Management
From Supply to Demand.
Beneficial for Business Efficiency- Concise use of Resources at Optimal level
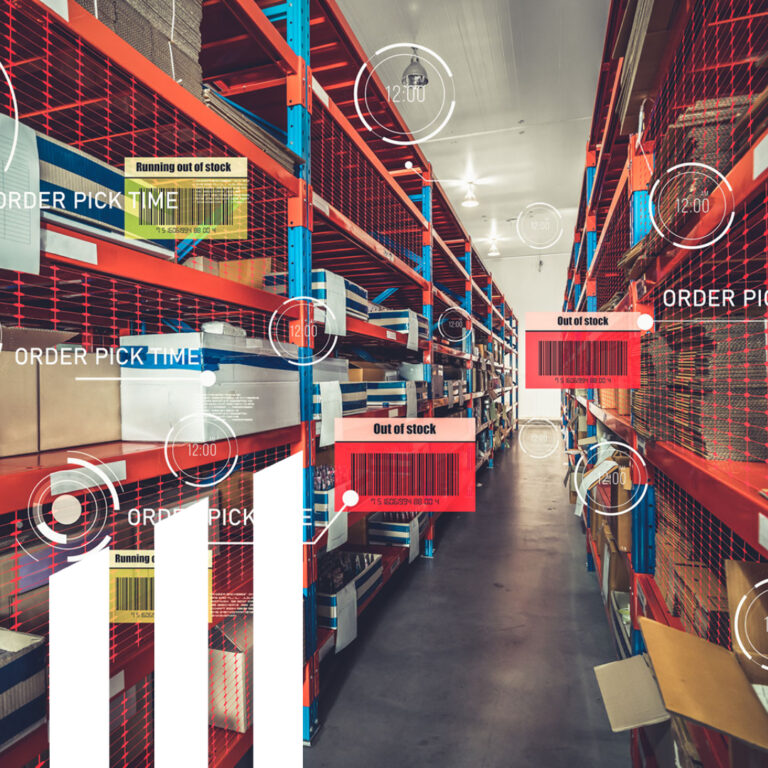
Benefits of RFID In Supply Chain Management
When a firm expands its activities, its supply chain inevitably expands as well. The processes get increasingly complicated, emphasizing the need for accuracy at each supply chain link.
RFID technology can help you grow your operations with accuracy, precision, and scalability.
How can you use RFID technology in your supply chain management operation?
- Freight and supply chain logistics
- Inventory Management
- Vehicle Tracking
- Assest Tracking
RFID technology has made it feasible to automate the receiving of commodities from warehouses and distribution centers all around the world, all in one system. This comprises both producer deliveries and shop returns of previous collections.
Within the RFID tunnel, all commodities received into the distribution facility are registered. The readings can then be used to determine whether the multipack is similar, eliminating the need to unpack individual cartons for delivery.
Limited visibility combined with mistakes can put a company’s production on hold and reduce its overall efficiency. Radio frequency identification is one method that emerged to solve these problems in recent years.
RFID benefits in the supply chain are frequently underrated. They are often perhaps more beneficial than most people know. The upside for implementing RFID technology for any operation is immense, and that’s especially true in Supply Chain Management.
RFID Technology in Supply Chain Management
The role of RFID in supply chain management is very broad and comprehensive. RFIDs are beneficial for increasing business efficiency. In terms of management, RFID enables for better decision-making based on consumer needs and more efficient use of company resources.
RFID in supply chain management enables real-time information access while also lowering the time and effort necessary for data collection. Real-time automated identification and data capture technologies, such as RFID devices, are important for rapid manufacturing. RFID gives real-time information on all material stockpiles and Work-In-Process.
RFID contributes to the supply chain operations by providing unique object identification and real-time information. As a result, RFID improves data accuracy, accelerates processes, enables product traceability and visibility, increases physical flow speed, and reduces work-in-progress and inventories.
The use of RFID technology simplifies process automation and enhances operations management by reducing workload and eliminating human errors.
Applications of radio frequency identification (RFID) technology within supply chain management have received particular attention in the past few years, some of its applications include:
- Solving production material demand problem in manufacturing environment hospitality
- Tracking vehicles in an automotive manufacturing plant shipment yard
- Prevention of collision accidents with heavy equipment
- Real-time warehouse operation planning system
- Monitoring quality in food logistics
- Fashion product development
- Farm management systems
- Parking management
- Traffic management
- Service Sector
- Construction
- Maintenance
- Healthcare
Supply Chain Tracking
RFID can track the precise position of an object as well as its technical state. Aside from that, the RFID identification technology is used to label items, raw materials, and finished products for industrial and commercial records.
This allows daily labor in the domains of production, trade, and business to be completed considerably faster and more accurately. Logistics and transportation in the RFID system get insight into the supply chain, allowing for more effective distribution channel management and, as a result, lower operating costs. The risk of items being falsified from the producer to the customer is eliminated when the supply chain is tracked.
Using the data obtained with the help of RFID in logistics and supply chain can decrease expenses is one of the most significant advantages of improved visibility. This shows the most precise inventory levels at all times.
Companies can use RFID to determine how much merchandise they have on hand. This form of real-time tracking allows them to better plan when to reorder in order to replenish inventory.
It also assists them in determining the optimal inventory level, ensuring that no goods are left on the shelves wasting money on storage. While maintaining adequate inventory levels may not appear to be a profit driver, it can help a company save between 20% to 30% on warehousing and storage expenditures.
Retailers who have already integrated RFID into their operations are reaping the rewards. They are having less troubles with out-of-stock products and are boosting the availability of their products on the shelf. RFID can scan each unique SKU number and identify product variances like size, color, and style.
Manufacturers may more easily raise inventory count rates from 200 to upwards of 12,000+ items every hour with RFID-tagged merchandise (of course, this is contingent on how things are housed and how accessible they are to reach).
This kind of transparency informs retailers about what is selling and what has been lying on their shelves for far too long to be considered lucrative. When dealing with a large number of product units, this type of task would take days or weeks to complete without RFID, whereas it may be completed in minutes with RFID.
Increases Efficiency
RFID employs radio frequencies to ‘ping’ the product’s location. RFID tags cut the time it takes to find and track things in half. This mechanism reduces the amount of time spent looking for items, which positively reflects on personnel expenses and can enhance overall facility productivity.
Keeping that in mind, RFID technology increase efficiency in the entire supply chain process by:
RFID has made significant progress in terms of inventory accuracy and count accuracy. RFID can take in a much larger range of data much more quickly than human inventory counts. You can conduct inventory counts in minutes because no direct line of sight is necessary.
You can keep track of progress by strategically deploying RFID readers around your warehouse. This can increase manufacturing efficiency while also giving real-time inventory insight, allowing you to conveniently check inventory levels and reduce shrinkage. If you need to track expensive containers, pallets, or even individual assets, this is a good option. You can see when products enter and depart your facility in real time.
Because RFID doesn’t require a direct line of sight, workers don’t have to search for and scan each barcode individually. You may save time and almost eliminate human mistakes by automating your data collection methods.
When you install sensors at the entrance, workers can drive forklifts full of inventory and assets into your warehouse, and the system will automatically scan all RFID tags as they pass by. Inventory items do not need to be numbered and scanned individually because no direct line of sight is required. RFID tags could efficiently replace barcode labels, making data collection and warehouse automation more efficient.
Unlike barcodes, RFID technology not only tells you if an item has been received or is in stock; it also tells you where it is, which decreases inventory errors caused by lost inventory and dramatically improves manufacturing productivity. Because this strategy enhances both accuracy and security while also helping to promote productivity within your operation, the value of RFID grows in tandem with the value of the object being tracked.
RFID sensors can be deployed in a number of locations across the warehouse, allowing workers to locate orders using the nearest sensor. This speeds up the delivery process by allowing merchandise to be located quickly without requiring personnel to spend time tracking down orders. If it isn’t in the right area, you’ll have to search the entire warehouse for it. Orders can be processed and dispatched in a short amount of time.

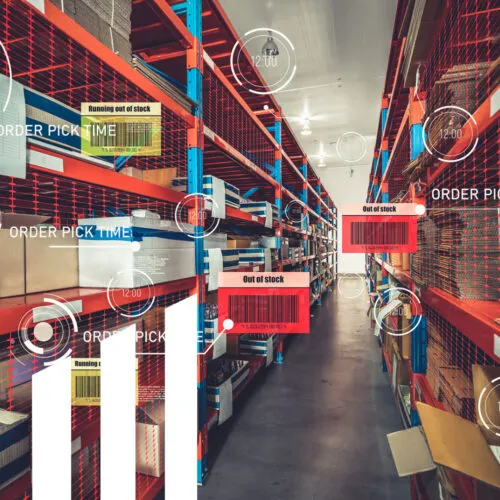
Usage of Safety Lights for Warehouses
The management of supply chains is reliant on warehousing. Your business strategy may be influenced by how you keep and handle your goods. General warehouses and distribution warehouses are the two popular types of warehouses large, small and medium enterprises use.
As backup inventory, seasonal products are held in general warehouses. Customer service is limited, and handling and transportation are also constrained. Distribution warehouses, on the other hand, offer a wide range of short-term storage options.
Handling, distribution, transportation, and order fulfillment are among them.
RFID Forklift Safety Warning System is the easiest and most simple solution for improving forklift safety in your warehouse or distribution center.
There are three main reasons to consider an RFID Forklift Safety Warning System:
- It is the easiest system to install and set up. It can operate as a standalone system and does not require any software or IT involvement to set up.
- It will significantly increase safety in high traffic areas where blind spots are a potential hazard.
- It can easily be configured to accommodate as many forklifts or vehicles as you need by simply purchasing more RFID tags.